Little John
Drone Bee
- Joined
- May 27, 2012
- Messages
- 1,655
- Reaction score
- 4
- Location
- Boston, UK
- Hive Type
- Other
- Number of Hives
- 50+
I see there's been some interest here in the quality of Mann-Lake's boxes - so here's my input on this ....
Last year I took delivery of a hundred quid's worth of 'standard' (i.e. seconds) cedar brood boxes. This shows some examples of the knots in them:
Now knots in the sides or front/back panels don't matter very much, but knots in the rails are really bad news, as rails can become warped as a result.
My plan was to cut-up these boxes to make 5-frame nucs - but - I didn't fully appreciate how much of a problem this warping of the rails would become. I decided to build the boxes first, and then sort out any problems later - which was a HUGE mistake.
Here's a shot of the glued boxes:
New sides were then added using Oregon Pine Studs recovered from pallets, with glued and screwed butt joints, and grooves cut into the inner sides for feeder-dividers so that they can be used either as 5-frame nucs or as dual half-size-frame mating nucs.
It was at this point that the 'warped rails' problem became evident, as the gap between the new sides (which were precisely 225mm ) and the rails became obvious:
But - there was a further problem, in that as most of the rails were concave on their outer edges, and that as this concavity wasn't necessarily equal around a central point, there was no longer any reference surface by which to machine this error out. So - I was forced to hot-glue the original sides together back-to-back, and approximate as equally as possible the resulting 'rock'.
Strips of filler wood were then glued on, and the upper and lower surfaces finally machined flat. This of course, was a lot of farting about. But - lesson learned - machine any warped rails straight BEFORE assembly, not afterwards.
Then filler was applied, sanded down and the boxes finally painted with industrial floor paint.
Ok - latest update ...
I took delivery this morning of another 20 Mann-Lake flat-pack brood boxes - in pine this time, not cedar - only to discover that these boxes (as supplied) are not the same 'design': the cedar boxes were bottom-bee-space and had angled edges to the front/back panels, eliminating the need to fit runners.
These pine brood boxes are almost bottom-bee-space, except the bottom rails do not have the correct profile for b/b-s. With runners fitted and the bottom rails re-profiled, they would then become b/b-s ; with the bottoms of the front/back panels padded-out and no runners fitted to their tops, they could then be run as top-bee-space. But as delivered, they are neither - so if you're planning on just slotting these together 'as received', you'll be disappointed.
The boxes are being sold at a very low price, and are fair value for money - but you really do need some woodworking machinery to make them serviceable.
LJ
Last year I took delivery of a hundred quid's worth of 'standard' (i.e. seconds) cedar brood boxes. This shows some examples of the knots in them:

Now knots in the sides or front/back panels don't matter very much, but knots in the rails are really bad news, as rails can become warped as a result.
My plan was to cut-up these boxes to make 5-frame nucs - but - I didn't fully appreciate how much of a problem this warping of the rails would become. I decided to build the boxes first, and then sort out any problems later - which was a HUGE mistake.
Here's a shot of the glued boxes:
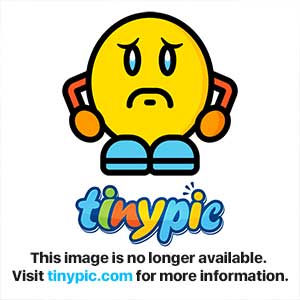
New sides were then added using Oregon Pine Studs recovered from pallets, with glued and screwed butt joints, and grooves cut into the inner sides for feeder-dividers so that they can be used either as 5-frame nucs or as dual half-size-frame mating nucs.
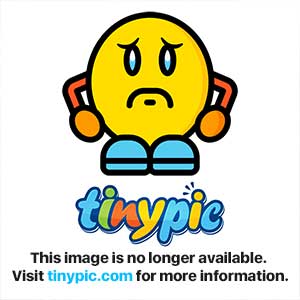
It was at this point that the 'warped rails' problem became evident, as the gap between the new sides (which were precisely 225mm ) and the rails became obvious:
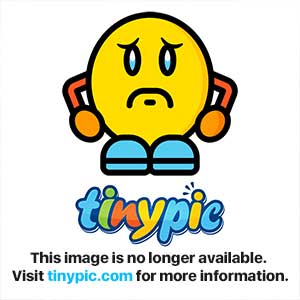
But - there was a further problem, in that as most of the rails were concave on their outer edges, and that as this concavity wasn't necessarily equal around a central point, there was no longer any reference surface by which to machine this error out. So - I was forced to hot-glue the original sides together back-to-back, and approximate as equally as possible the resulting 'rock'.
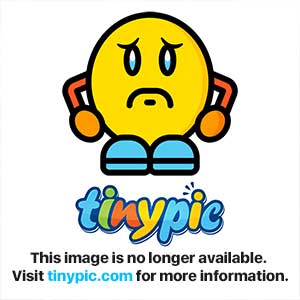
Strips of filler wood were then glued on, and the upper and lower surfaces finally machined flat. This of course, was a lot of farting about. But - lesson learned - machine any warped rails straight BEFORE assembly, not afterwards.
Then filler was applied, sanded down and the boxes finally painted with industrial floor paint.
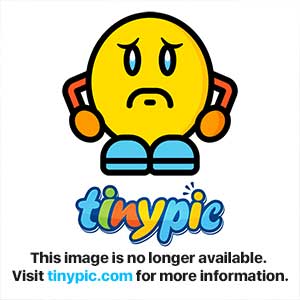
Ok - latest update ...
I took delivery this morning of another 20 Mann-Lake flat-pack brood boxes - in pine this time, not cedar - only to discover that these boxes (as supplied) are not the same 'design': the cedar boxes were bottom-bee-space and had angled edges to the front/back panels, eliminating the need to fit runners.
These pine brood boxes are almost bottom-bee-space, except the bottom rails do not have the correct profile for b/b-s. With runners fitted and the bottom rails re-profiled, they would then become b/b-s ; with the bottoms of the front/back panels padded-out and no runners fitted to their tops, they could then be run as top-bee-space. But as delivered, they are neither - so if you're planning on just slotting these together 'as received', you'll be disappointed.
The boxes are being sold at a very low price, and are fair value for money - but you really do need some woodworking machinery to make them serviceable.
LJ