ugcheleuce
Field Bee
- Joined
- Apr 15, 2013
- Messages
- 669
- Reaction score
- 1
- Location
- Apeldoorn, Netherlands
- Hive Type
- National
- Number of Hives
- 7-10
Hello everyone
I have no idea what to christen this hive, so... it's a three-piece lugrest wall hive. I'm going to make about 10 of these (I have that much wood). The key element is that the thick plank is 32 mm thick, and that is useful. I got a woodworking shop to saw the thick planks to the right dimensions and had them delivered in planks of about 1.5 m long. The idea is that I would use my little handsaw to saw them into the appropriate lengths when I know what thickness the side walls will have (and they can have different thicknesses).
Enough chatter, here are the images:
Step 1: eight planks per box
The eight planks are:
* Two thick pieces of wood, 32 mm thick, 100 mm tall, 394 mm long
* Four thin pieces of wood, 18 mm thick, roughly 5 cm tall, 394 mm long
* Two bigger pieces of wood (for the side-walls), 150 mm x 475 mm
(in the image above I have four pieces of left-over meranti but in the images below I used four pieces of left-over green painted spruce that I salvaged from a failed experimental hive, so don't scratch your head and wonder what happened to the meranti in the other pictures)
Step 2: make the profiled front/rear walls (where the lugs will rest)
I know the space underneath the lug rest is rather large, but that is because the thick plank comes in a standard 200 mm size and if the woodworker cuts it in half, I can get twice as many supers from it. If the extra room is an issue, I can fill it up with small pieces of wood. In the current design, there is 27 mm space above the lug rests and 18 mm (BR) or 23 mm (HN) below it.
Step 3: glue and measure
Step 4: nail with small nails, and make it right angles
Two advantages of this method for me are: it doesn't matter what size the thin planks on the front/rear of the hive is, as long as they are the right length; and I can make any size hive (or use any width side wall) with the minimum of required measurement adjustments elsewhere in the design.
Samuel
I have no idea what to christen this hive, so... it's a three-piece lugrest wall hive. I'm going to make about 10 of these (I have that much wood). The key element is that the thick plank is 32 mm thick, and that is useful. I got a woodworking shop to saw the thick planks to the right dimensions and had them delivered in planks of about 1.5 m long. The idea is that I would use my little handsaw to saw them into the appropriate lengths when I know what thickness the side walls will have (and they can have different thicknesses).
Enough chatter, here are the images:
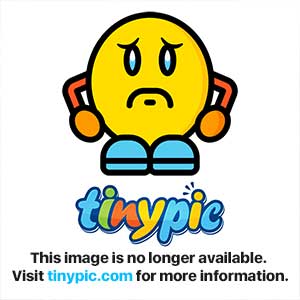
Step 1: eight planks per box
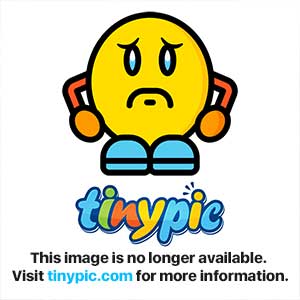
The eight planks are:
* Two thick pieces of wood, 32 mm thick, 100 mm tall, 394 mm long
* Four thin pieces of wood, 18 mm thick, roughly 5 cm tall, 394 mm long
* Two bigger pieces of wood (for the side-walls), 150 mm x 475 mm
(in the image above I have four pieces of left-over meranti but in the images below I used four pieces of left-over green painted spruce that I salvaged from a failed experimental hive, so don't scratch your head and wonder what happened to the meranti in the other pictures)
Step 2: make the profiled front/rear walls (where the lugs will rest)
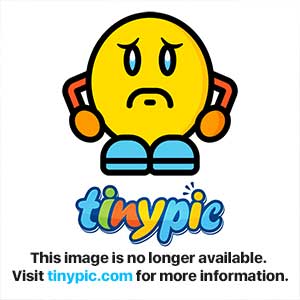
I know the space underneath the lug rest is rather large, but that is because the thick plank comes in a standard 200 mm size and if the woodworker cuts it in half, I can get twice as many supers from it. If the extra room is an issue, I can fill it up with small pieces of wood. In the current design, there is 27 mm space above the lug rests and 18 mm (BR) or 23 mm (HN) below it.
Step 3: glue and measure
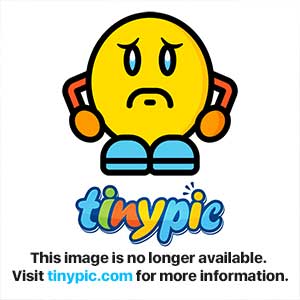
Step 4: nail with small nails, and make it right angles
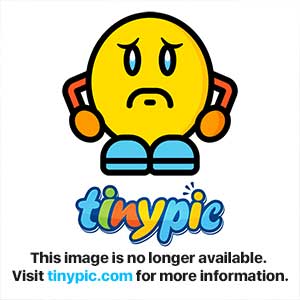
Two advantages of this method for me are: it doesn't matter what size the thin planks on the front/rear of the hive is, as long as they are the right length; and I can make any size hive (or use any width side wall) with the minimum of required measurement adjustments elsewhere in the design.
Samuel
Last edited: